Data Conditioning 101 – How Chemical Companies Are Turning Messy Data into Actionable Insights
Introduction
In today’s chemical and petrochemical industries, data is the new oil – a valuable resource to drive efficiency and innovation. But raw data coming from plant sensors, lab analyses, and ERP systems is often messy, inconsistent, and hard to trust. Before analytics and AI can work their magic, this raw information needs refinement. Enter data conditioning: the process of cleaning, validating, and reconciling data to turn it into high-quality information. Just as crude oil must be refined into fuel, chemical companies must refine their data so that decision-makers can truly rely on it. In this primer, we’ll explore Data Conditioning 101 – what it means, why it’s essential for chemical manufacturers, and how firms are leveraging it to turn messy data into actionable insights that boost production and profits.
The Challenge – Messy Data in Chemical Manufacturing
Chemical plants are data-rich environments, generating thousands of data points daily from flow meters, pressure sensors, temperature gauges, lab quality tests, inventory logs, and more. In theory, all this data should empower better decisions. In practice, many companies are drowning in data but starving for insights. Common data challenges include:
- Inconsistencies and Errors: Different sources often don’t agree. For example, the production volume recorded in an ERP might not match the total from individual flow meters, due to timing differences or measurement errors. It’s not uncommon to find significant mass or energy imbalances in process data – one case showed a -14.9% mass imbalance and -8.3% energy imbalance when comparing raw sensor data to expected totals. Such discrepancies make it hard to know the truth.
- Siloed Data and Manual Work: Operational data (from control systems or historians) may be isolated from business data (from ERP, lab, or supply chain systems). Engineers and analysts spend hours manually reconciling spreadsheets, entering adjustments, or emailing colleagues for missing info. This delayed, manual process means decisions are often based on stale or approximate data.
- Lack of Trust in Data: When data is known to be incomplete or frequently requires tweaking, teams lose confidence. People resort to using intuition or very high safety margins “just in case,” or they only trust certain “expert” individuals’ numbers. This culture of mistrust in data is a major barrier to digital transformation in the sector.
These issues lead to inefficiencies and missed opportunities. As Sigmafine’s petrochemical solution brief notes, data availability alone isn’t enough – “consistency and accuracy are imperative… data quality matters!! In other words, bad or inconsistent data will lead to bad decisions, even if you have a lot of it. This is where data conditioning comes in.
What is Data Conditioning?
Data Conditioning refers to the set of techniques and processes that ensure raw data is validated, error-corrected, and made consistent before use. Think of it as preparing your ingredients before cooking a meal – you clean, trim, and measure everything so the recipe turns out right. In a chemical plant context, data conditioning typically includes:
- Data Validation: Checking data against rules or expected patterns to identify suspect values. For example, if a flow meter suddenly reads zero when the plant is running, that’s likely an instrument fault or data drop-out. Validation routines flag such anomalies or any readings that violate physical laws (like a negative mass). Sigmafine’s software performs “data validation and reconciliation [to verify] the level of agreement among data sources and spot missing/incorrect data”. This step is about detecting bad data.
- Data Reconciliation: Adjusting and correcting data using mathematical models and conservation principles. This is the core of data conditioning in heavy industry. By applying first-principle balances (mass, energy, component balances) to the network of process data, reconciliation algorithms can identify and reduce errors in the measurements. The result is a balanced dataset that honors physical laws and is statistically adjusted to minimize errors. For instance, if five flow measurements around a unit don’t perfectly balance, reconciliation will distribute the error so that they close the balance, within confidence limits. One Sigmafine case study on an ammonia plant revealed a 15% imbalance that was resolved through such reconciliation. After conditioning, the mass balance came into near-perfect alignment, reducing that uncertainty.
- Data Fusion and Alignment: Combining data from disparate sources and aligning them in time and granularity. A common challenge is that different systems record data at different intervals (real-time vs. daily totals) or different contexts (one system logs by batch, another by continuous totals). Data conditioning involves integrating these sources into one coherent picture. For example, Sigmafine can take transactional data from an ERP (like a monthly production quantity) and split or align it with daily process data, so that operations and accounting see the same numbers just framed differently. It can also infer missing information (like estimating an unmeasured stream) based on the overall balance and known process characteristics. This ensures nothing is lost between systems.
In short, data conditioning turns “dirty” data into “refined, consistent and more accurate information to support your decision process.” It’s about making sure all the data makes sense together, is complete, and is reliable enough to base decisions on. The “single version of the truth” becomes a reality once data is conditioned – everyone from the control room to the boardroom is looking at the same validated numbers.
How Chemical Companies Apply Data Conditioning
Leading chemical and petrochemical companies are already leveraging data conditioning to great effect. Here’s how it’s making a difference:
- Daily Production & Inventory Accountability: Instead of waiting until month-end to reconcile production figures (and struggling with “misalignments at the end of the month” between plants or business units), companies use data reconciliation near real-time. For example, the integrated refinery-petrochemical complexes model all material movements (feeds, products, inter-unit transfers) in Sigmafine. By doing so, they get not just the daily balanced material inventory and production report, but can reduce it to 10-15 minutes of automatic updates, approaching near real-time. This means no more end-of-month surprises – losses, errors, or unaccounted volumes are caught early on and can be investigated immediately. One benefit is smoother operations and trust between departments (operations, finance, and supply chain all agree on the numbers).
- Improving Plant Performance KPIs: Data conditioning provides accurate data for calculating performance metrics like yield, energy efficiency, and throughput. For instance, when raw data is used, energy KPIs might look erratic or misleading due to sensor biases. After reconciliation, key performance indicators (KPIs) reflect reality with much lower variance, so trends and deviations stand out clearly. Chemical companies apply this to monitor equipment efficiency (e.g., distillation column or reactor performance). If a KPI drifts, they know it’s a true change and not just a data error. As Pimsoft describes, “model based KPIs you can rely upon to make decisions” become possible. This gives engineers confidence to optimize processes based on data.
- Enhanced Planning & Forecasting: With cleaner data and a unified dataset, planners can update their models more frequently. An example from a Sigmafine user: planning updates that used to happen weekly or monthly can shift to daily. When planners trust that yesterday’s production figures are right, they can adjust the production plan or feedstock allocation sooner. This agility can save a lot of money – e.g., avoiding overproduction of a chemical that’s nearing storage limits, or reallocating feeds to more profitable products in near-real-time. Better data shortens the feedback loop.
- Regulatory Compliance and Sustainability: Environmental and compliance managers also benefit. Data conditioning ensures emission calculations or mass balance reports (e.g., for a pollution inventory or a carbon footprint) are based on solid data. In an era of strict environmental reporting, having an auditable, traceable data trail is invaluable. Sigmafine’s approach provides a “traceable and auditable source of data for complete transparency” in material and energy balances. Companies can confidently report numbers to regulators knowing they’ve been validated, and they can more easily track metrics like how much recycled material is in final products or what the true plant-wide energy consumption is.
Getting Started with Data Conditioning
Implementing data conditioning might sound complex, but tools and best practices have matured. Here are steps to consider for a chemical manufacturer looking to turn data into insights:
- Identify Critical Data and Pain Points: Focus on an area where data issues are causing headaches – for example, production accounting discrepancies, unclear loss yield, or an energy efficiency program hindered by unreliable data. Learn more about the types of data defects in our earlier blog on data conditioning. Quantify the impact (e.g., “We can’t reconcile 5% of our raw material usage” or “Lab vs sensor data often differs by X”). This builds the case for investing time in data conditioning.
- Use a Model-Based Approach: Map out the process or system with a data model. Modern data conditioning uses a “digital twin” of the plant’s mass and energy balances. Sigmafine, for instance, “puts in relation raw process data, material transactions and business data in one model constrained by first principles equations”. By modeling the process (tanks, reactors, flows), you provide a structure to check the data against (like ensuring input = output for each node).
- Leverage Specialized Software: While manual reconciliation in spreadsheets is possible, it’s not scalable or sustainable. Industrial software like Sigmafine automates much of the validation and reconciliation, and can run continuously or in defined intervals. These tools handle the heavy math and also provide diagnostic reports highlighting where the biggest data issues were found (e.g., which instruments might be miscalibrated if they consistently required adjustment). Using such software, one petrochemical site improved the quality of its real-time data feeds, feeding reconciled data directly into their BI tools. The result was that engineers and even machine learning algorithms could trust the data coming in, leading to more effective optimizations.
- Establish Governance and Process: Data conditioning isn’t a one-off project; it becomes a routine part of operations. Companies that succeed often designate a data champion or a small team (perhaps within the operations excellence or digital transformation group) to maintain the data models, review reconciliation results, and work with plant personnel to fix underlying issues (like a bad meter) that the reconciliation flags. Over time, as data quality improves, the reconciliation adjustments get smaller – a sign that the plant’s instrumentation and data management have improved.
- Integrate with Decision-Making: Finally, ensure the conditioned data actually flows to the people and systems making decisions. This might mean pushing the reconciled data back into the data historian or into dashboards that production engineers use daily. When everyone from the boardroom to the control room is using the conditioned, single-source data, the organization truly becomes data-driven. As one of Sigmafine’s solution pillars states: “Improve data quality for better business decisions” - high-quality data should inform strategic and tactical decisions alike.
Conclusion – Turning Insights into Action
Data conditioning is the unsung hero behind successful analytics and optimization in chemical manufacturing. It transforms the chaotic, “dirty” data that plants inevitably generate into a trustworthy foundation for decision-making. By investing in data quality – through validation, reconciliation, and proper data management – chemical companies unlock actionable insights: they can identify inefficiencies faster, adjust to changes in feedstock or demand more nimbly, and squeeze more performance out of their assets with confidence.
In this primer, we introduced the why and how of data conditioning. To dive deeper and see real examples in action, watch our webinar “Better Data, Better Decisions: How Chemical Plants Are Leveraging Data Conditioning to Optimize Production” on May 29, 2025 – For webinar recording, click here. You’ll hear experts discuss case studies and strategies, and get practical tips to start improving your own data. Better data does lead to better decisions – and in a competitive industry, better decisions make all the difference. Or talk directly with our Data Experts by clicking here.
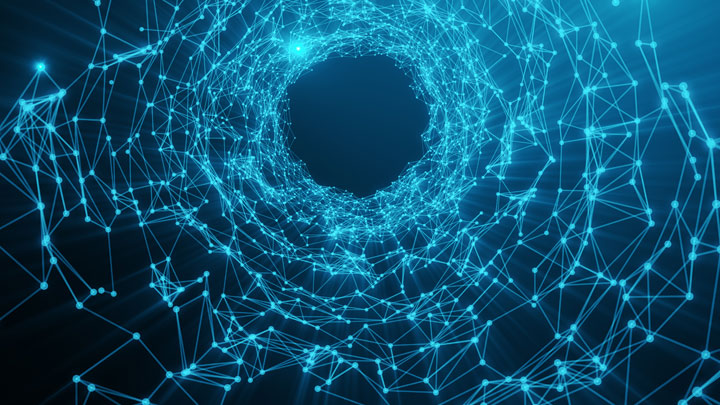
Trusting Data for Action
In process and manufacturing, information systems should be implemented with a system of checks and balances to maximize the quality of data and the economic potential of data. Creating an environment where data can be trusted is not an afterthought. Data quality, similar to product quality, needs to be built into our business and data management activities so that we can trust data for action at all times.
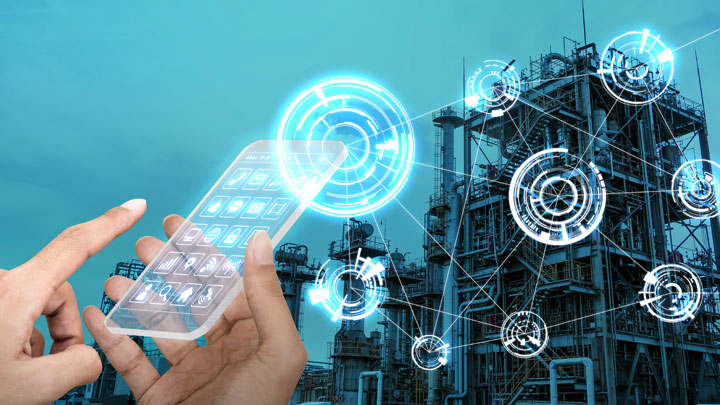
Transforming Data into Digital Assets
Being digital refers to data and information stored digitally. Being an asset refers to having control of the data and information to produce positive economic value. Being a digital asset consequently refers to data & information we own and control and from which we can generate sustainable and tangible benefits. This has been the job of Sigmafine and its users for almost three (3) decades now.