Workflow Planning in Oil and Gas: Why Data Quality Is the New Competitive Advantage
Q: Why is high-quality process data critical for refinery workflow planning?
A: In oil refining, missing or inaccurate data comes at a high cost. Without trustworthy process data, planning and decision-making suffer – leading to unaccounted losses, regulatory compliance risks, and suboptimal operations. Gartner research shows poor data quality costs companies ~$12.9 million per year on average! Refinery-wide mass balance calculations illustrate this: they provide accurate accounting of all inputs, outputs, and inventories, reducing discrepancies (and thus losses) that directly impact profitability. Tools like Sigmafine are purpose-built for this kind of data validation and reconciliation, helping refiners ensure consistency, completeness, and credibility across their process data. Conversely, poor data quality means managers and engineers lack confidence in reported production figures, making it harder to optimize workflows or identify issues. As a recent industry presentation aptly titled, “The High Cost of Missing or Inaccurate Data in Workflow Planning: How to Improve Operational Decisions in Oil & Gas,” unreliable data undermines operational decisions. In short, high-quality process data is the backbone of effective refinery planning – it enables accurate performance analysis, proactive maintenance (e.g. scheduling flowmeter calibrations), and informed strategic initiatives. Even safety and compliance depend on data fidelity; for example, being able to verify mass balance closure within accepted thresholds gives confidence in environmental and financial reporting standards. All of these factors make high-quality data not just a technical necessity, but a strategic asset for refining businesses.
Q: How does data reconciliation support digital refinery transformation?
A: Digital refinery transformation relies on data that is both abundant and reliable. Simply collecting big data from sensors isn’t enough – refineries must validate and reconcile that data into a usable form. Data reconciliation is crucial for turning real-time data streams into accurate, actionable insights. According to Emerson Automation, having accurate mass balance and yield accounting data is “a critical business practice to mitigate financial risk and reduce losses” as companies embrace digital transformation. In practice, this means that when all flow measurements and inventories are validated, a refinery can confidently feed data into advanced analytics, predictive models, and digital twin simulations. Real-time digital initiatives depend on data quality – without it, even the best analytics will output nonsense. In short, process data quality is the foundation of the digital refinery. By reconciling data and closing the plant-wide mass balance each day, refiners establish a single source of truth that decision-makers across the organization can trust for optimizing production, energy use, and business outcomes, and is a key component of production accounting in process industries. This data integrity paves the way for automated workflows, better forecasting, and enterprise-wide visibility – all key goals of digital transformation in the oil & gas sector.
Q: What is Sigmafine and how does it improve refinery process data quality?
A: Sigmafine is an industrial software platform (by Pimsoft) designed specifically to validate, reconcile, and condition process data for enterprises like oil refineries. Essentially, Sigmafine acts as a digital mass balance engine: it takes in all the raw measurements (flows, tank levels, temperatures, etc.) and uses data reconciliation algorithms to correct errors and align the data with physical reality. The result is a set of validated, “trustworthy” numbers that engineers and business systems can rely on. Sigmafine is used daily in complex refineries with many production units, tank farms, and thousands of flow meters, delivering reconciled data for accurate production and yield accounting. It flags bad or inconsistent values – for example, a faulty flowmeter reading or a “noisy” tank level gauge – and identifies gross errors that violate conservation rules. By tracing these data issues back to their source (down to specific units or instruments), Sigmafine helps engineers fix them promptly (e.g. replacing a sensor or correcting an input). The platform then adjusts the data to close any material imbalances. In fact, Sigmafine defines a metric (often called DX1) to measure how much correction is needed to close the refinery’s mass balance, with a best-practice target of <5% adjustment. When the data falls within such targets, it indicates high fidelity. The benefits of this improved data quality are far-reaching: Sigmafine essentially automates and audits the production accounting process, ensuring that the reported figures for raw material consumption, production output, and losses are accurate and auditable. It also supports operational analytics – for instance, by validating key performance indicators (KPIs) used for process control and optimization. Want to learn more how you can improve the data quality in your production process –talk to our Data Experts.
Q: How has Astron Energy improved refinery performance with Sigmafine? (Case Study)
A: A great real-world example is Astron Energy, that owns and operate South Africa 2nd largest crude oil refinery located in Cape Town with a capacity of 100,000 barrels a day, and has leveraged Sigmafine to transform its accounting and planning workflows. Before Sigmafine, Astron’s mass balance was largely manual – they relied on Excel spreadsheets for monthly stock reconciliation, which was labor-intensive and error-prone. Upon implementing Sigmafine, they immediately moved to daily mass balancing and automated much of the data gathering and validation. Astron also replaced a legacy oil movement tracking system with Sigmafine’s Intelligent Movement Management (IMM) module. Hear more about their journey in this recent webinar here.
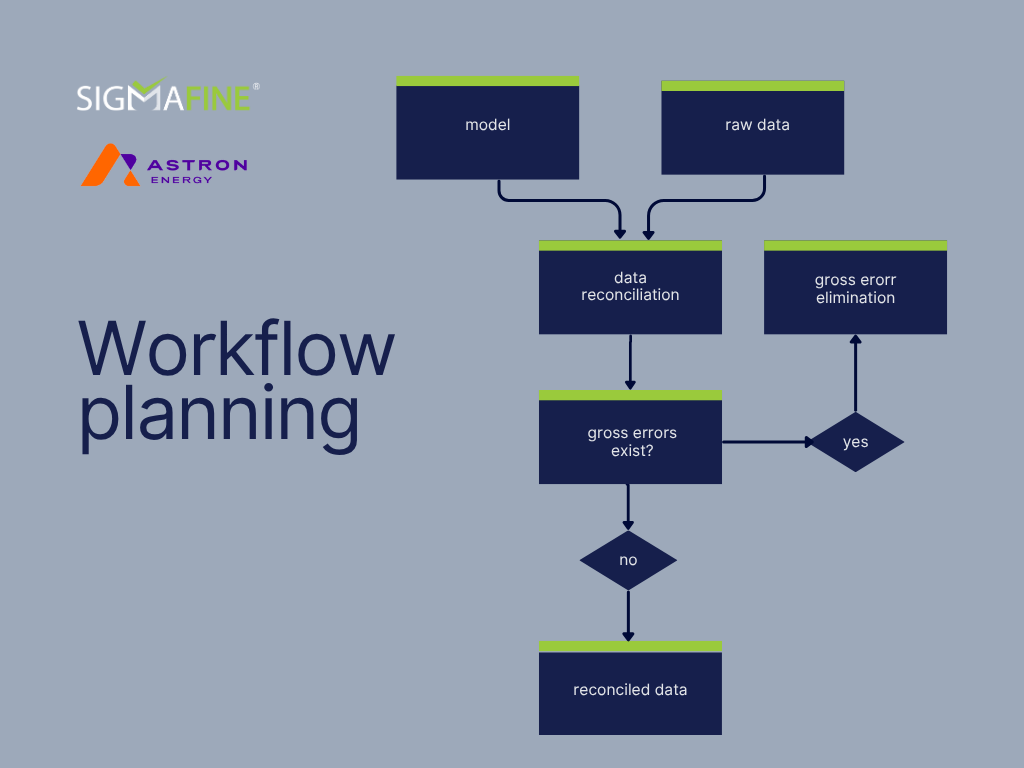
According to Astron’s refinery mass balance engineers, Sigmafine is now used for daily production accounting and near real-time oil movement management, with the explicit goal of avoiding costly errors and finding cost-saving opportunities. One key improvement came from integrating Sigmafine with the refinery’s ERP (SAP) system: validated stock data now flows seamlessly into SAP at the start of each month, allowing Astron to close its monthly inventory and production balance much faster and with confidence. In fact, the inclusion of Sigmafine’s IMM led to rapid detection of any misalignments between recorded movements and actual tank inventories, so accounting discrepancies are caught and resolved in near real-time instead of weeks later. During a recent refinery shutdown (2020–2023), Astron paused Sigmafine updates, but upon restart they performed a full Sigmafine upgrade and model update to reflect all process changes before resuming operations. This highlights how essential the tool had become – running daily mass balances was considered a priority for reliable operations. Since coming back online, Astron reports several benefits from their “digital” mass balance workflow: improved volume tracking, easy identification of stock imbalances, reduced manual data input, and confidence that product quality specs (used in volume correction calculations) are validated. In summary, Astron Energy’s case study shows that Sigmafine not only replaced error-prone manual processes with an automated, accurate system, but also enhanced their operational efficiency. The refinery can now trust its data to make decisions, whether it’s diagnosing a sudden yield loss or ensuring the books balance for corporate reporting.
Q: What results and business benefits can refineries achieve with Sigmafine?
A: Companies that invest in process data quality solutions like Sigmafine often see substantial operational and strategic gains. Losses are reduced and profitability improves: by reconciling data and pinpointing previously unknown losses (e.g. measurement errors, unaccounted shrinkage), refineries can tighten their material balances. In one case, an Asian refinery (Pertamina Unit VI Balongan) integrated Sigmafine into its oil accounting system and managed to cut its calculated working loss and total loss by up to 36%, directly reducing production costs. Similarly, global majors have deployed Sigmafine across multiple sites – for example, Chevron uses Sigmafine at all its refineries as part of a gross margin improvement initiative, ensuring each site is operating based on the same accurate data standards. Another benefit is greater trust and transparency in data. Some refiners have implemented Sigmafine specifically to build confidence among stakeholders (even external ones like finance partners or regulators) by showing that inventory and production figures are validated and credible. Operational excellence is a recurring theme: Sigmafine users achieve daily automated production accounting (eliminating the need for manual reconciliations each morning), proactive identification of equipment issues (through data quality indicators that highlight, say, a drifting meter), and more efficient yield and energy management. Many report that this well-conditioned dataset enables better production planning and logistics optimization across the enterprise. In terms of strategic ROI, Sigmafine’s value proposition is compelling – it’s estimated to pay for itself in under 6 months on average, thanks to the combination of loss reduction, time savings, and improved decision-making. From a compliance and sustainability standpoint, high-quality data also helps meet environmental and corporate governance targets (for example, accurate emissions and energy usage data for ISO 50001 compliance can be ensured). In short, refineries leveraging Sigmafine have moved into a new era of data-driven operations: they can trust their numbers, respond quicker to problems, and continually improve processes based on reliable insights. This translates to not only immediate cost savings but also long-term competitive advantage in an industry pushing for digital transformation and efficiency.
Q: How can our refinery get started with improving process data quality?
A: Improving data quality starts with recognizing that your mass balance and production data can be a strategic asset – and then taking action to systematically improve it. A good first step is to evaluate your current production accounting and data reconciliation workflow: How much is done manually? Where do data inconsistencies arise? This gap analysis will highlight opportunities for improvement. Modern software solutions like Pimsoft’s Sigmafine are specifically designed to fill these gaps. By implementing Sigmafine (or a similar digital refinery data validation tool), you create a framework to automatically check and correct your data before it’s used in planning or reporting. To explore this further, we recommend seeing Sigmafine in action – you can book a Sigmafine demo or speak with the Sigmafine team to understand how it would fit into your refinery’s infrastructure. (For example, Sigmafine easily integrates with existing systems like OSIsoft PI for data historians and SAP for business systems, so it can slot into your current IT landscape with minimal disruption.) Engaging with Sigmafine experts can help you estimate the potential benefits for your operation – whether it’s reducing unaccounted losses, automating a tedious monthly reconciliation process, or improving multi-site data consistency. Now is the time to leverage your process data for strategic gain. Many refineries worldwide are already using Sigmafine to “drive daily business, account for material, report inventory, and support corporate governance” in their organizations. Your refinery can do the same – by investing in data quality today, you set the stage for digital transformation success tomorrow. Contact us to schedule a Sigmafine demo, talk to our consultants, or access additional resources and case studies on Sigmafine’s Oil & Gas solutions.
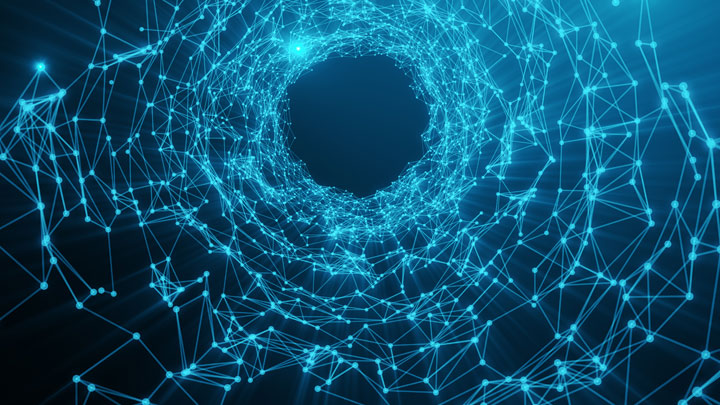
Trusting Data for Action
In process and manufacturing, information systems should be implemented with a system of checks and balances to maximize the quality of data and the economic potential of data. Creating an environment where data can be trusted is not an afterthought. Data quality, similar to product quality, needs to be built into our business and data management activities so that we can trust data for action at all times.
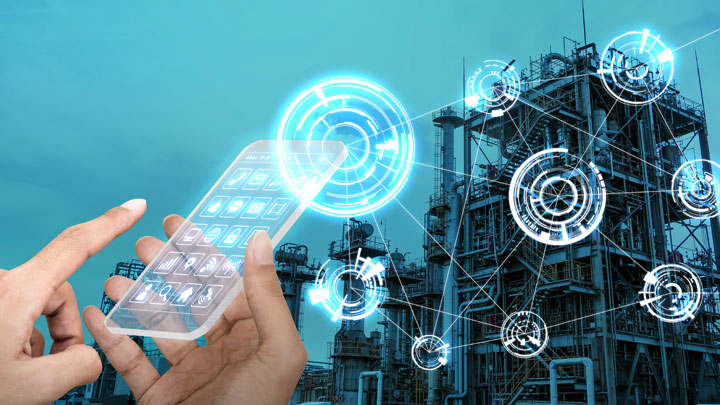
Transforming Data into Digital Assets
Being digital refers to data and information stored digitally. Being an asset refers to having control of the data and information to produce positive economic value. Being a digital asset consequently refers to data & information we own and control and from which we can generate sustainable and tangible benefits. This has been the job of Sigmafine and its users for almost three (3) decades now.